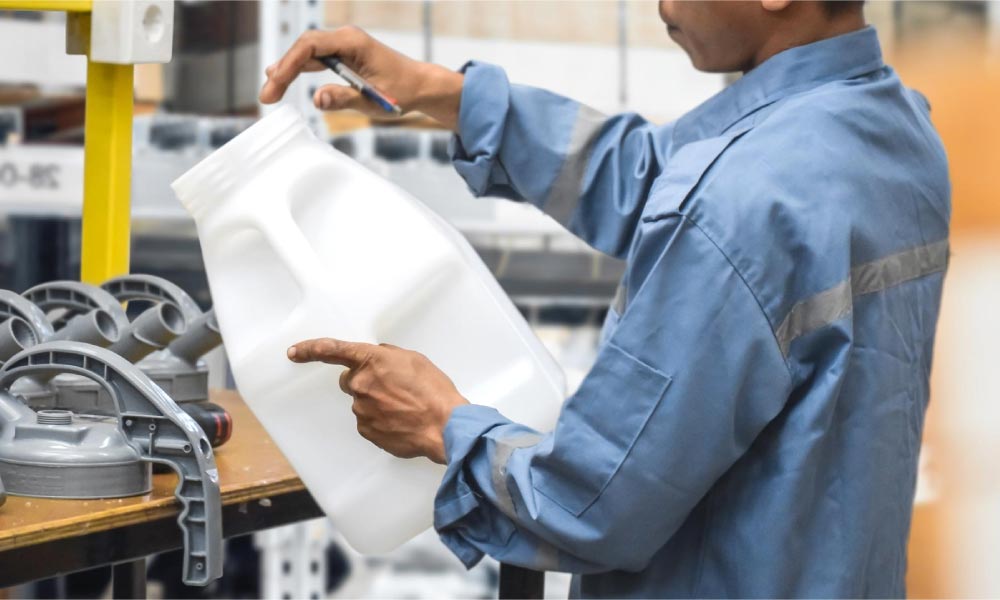
Complete Guide: What is an Oil Transfer Container and Its Benefits
I’ve always been fascinated by how a simple tool can change the game in industrial operations. If you’ve ever struggled with oil spills or contamination issues during lubricant transfers, you’re not alone. I too have experienced the challenges of managing oil in an industrial setting, and that’s why I’m excited to share this comprehensive guide with you.
In this guide, I’ll dive into the world of Oil Transfer Containers, discussing everything from what they are to how they benefit our day-to-day operations. I’ll walk you through design features, proper maintenance tips, and even share insights on selecting the right container for your needs. So, if you’re ready to transform your approach to handling oils, join me on this journey.
Working in the field, I’ve seen firsthand how neglecting the proper management of oil transfer can lead to costly and hazardous consequences. Contaminated oil can harm machinery, reduce efficiency, and even pose environmental risks. This guide is my way of sharing practical tips and insights that have helped me and many others overcome these challenges.
What is an Oil Transfer Container?
An Oil Transfer Container is a specialized tool designed for the safe, easy, and clean handling of lubricants. I first learned about these containers when I was struggling with makeshift solutions that just didn’t cut it. According to an article from Precision Lubrication, these containers are essential for transferring lubricants from bulk storage to application points without compromising cleanliness or safety citeturn0file0.
I’ve come to appreciate that an Oil Transfer Container isn’t just a simple bucket or can. It’s a carefully engineered product that plays a critical role in maintaining oil quality. When I first started using one, I was amazed at how much easier it made the process of lubrication, reducing spills and contamination risks.
At its core, an Oil Transfer Container is built to ensure that oil remains free from dirt, dust, and other contaminants. The design is focused on maintaining the integrity of the lubricant from storage to use. This is vital because even minor contamination can affect machine performance and longevity.
The Importance and Benefits of Oil Transfer Containers
When it comes to managing industrial lubricants, I’ve realized that the benefits of using Oil Transfer Containers are numerous. First and foremost, they help prevent contamination. Using a container that is designed specifically for oil transfer minimizes the risk of mixing different oils, which could lead to equipment damage.
There’s also the benefit of safety. I have seen how traditional methods, like using open-top cans or repurposed containers, often lead to spills and accidents. According to industry experts, a dedicated Oil Transfer Container is engineered with leak-proof designs and tight-sealing lids to ensure that spills are kept to a minimum. This not only protects the machinery but also creates a safer work environment for everyone involved.
Another advantage is the efficiency they bring to daily operations. When oil is transferred cleanly and safely, it saves time and reduces the need for constant clean-ups. This means less downtime for maintenance and more productivity on the floor. In my experience, switching to specialized oil transfer containers has led to smoother operations and a noticeable reduction in unexpected maintenance issues.
Furthermore, using these containers helps maintain the overall quality of the lubricant. Clean oil means better performance and longer life for machines, which translates to cost savings over time. I remember reading about how even a minor contamination could result in significant operational disruptions, so investing in the right container is truly worthwhile.
Design Features That Set Oil Transfer Containers Apart
One of the things that struck me when I first examined an Oil Transfer Container was the attention to detail in its design. These containers are typically made from high-density polyethylene (HDPE), a material chosen for its excellent resistance to heat, chemicals, and impacts. I found this particularly reassuring because it means the container can withstand the demanding conditions of industrial environments.
According to Precision Lubrication, one of the standard characteristics of these containers is their leak-proof design. They come with tight-sealing lids and well-designed spouts that ensure a controlled dispensing of oil, keeping spills to a bare minimum. This is something I value highly, as it directly contributes to a cleaner and safer workspace.
Another key design element is portability. Many of these containers feature easy-to-carry handles and are crafted with ergonomics in mind. I’ve experienced the convenience of carrying these containers around the facility, which makes routine maintenance and oil top-ups much simpler. Their lightweight yet durable construction really makes a difference when you’re on the move.
I also appreciate that many Oil Transfer Containers have color-coded lids. This might seem like a small feature, but it goes a long way in preventing mix-ups between different types of lubricants. When you’re dealing with multiple oil grades, having a quick visual cue is incredibly helpful. In fact, I often use this feature to quickly identify the oil type I need without wasting time deciphering labels.
Types and Materials Used in Oil Transfer Containers
Over time, I’ve seen a variety of Oil Transfer Containers in use across different industries. They aren’t one-size-fits-all; instead, they are tailored to meet the specific needs of each operation. According to Micro-Lube, oil storage containers can be made from stainless steel or polyethylene, each with its own set of advantages.
Stainless steel containers are known for their durability and resistance to corrosion. They are an excellent choice for applications where the oil might be stored for longer periods. However, I’ve noticed that stainless steel, while robust, can be heavier and more cumbersome to transport in some settings.
On the other hand, polyethylene Oil Transfer Containers have become popular due to their lightweight nature and excellent chemical resistance. Their semi-transparent quality allows me to quickly check the oil level without having to open the container, which helps maintain its cleanliness. The thicker sidewalls and flexibility also mean that these containers can absorb impacts and resist damage better than some alternatives.
In my experience, the choice of material often comes down to the specific requirements of the operation. If you need a container that can withstand rough handling and is easy to move around, polyethylene might be the best option. Conversely, if you’re looking for something that will last for many years in a relatively stable environment, stainless steel could be the way to go.
How to Choose the Right Oil Transfer Container for Your Business
Choosing the right Oil Transfer Container can be a daunting task if you’re not familiar with the technicalities. I remember the days when I would purchase containers based solely on price, only to find out later that they didn’t meet the specific needs of my operations. It wasn’t until I took a closer look at the design and features that I realized how critical it is to choose the right product.
When selecting a container, consider the volume and the type of oil you’re handling. I always start by evaluating the scale of my operations. If you’re dealing with small amounts for frequent top-ups, a smaller container might be sufficient. However, for bulk transfers, you’ll need something larger and more robust.
I also pay close attention to the container’s material. As I mentioned earlier, HDPE is a popular choice because of its resilience. It’s important to ensure that the container’s material is compatible with the type of lubricant you’re using, as some oils may react with certain plastics. According to experts, ensuring compatibility can prevent issues like chemical degradation and contamination over time.
Another factor to consider is the ease of handling and maintenance. A container that is easy to clean and maintain will save you time and money in the long run. I always look for features like leak-proof spouts and secure lids, as these are crucial for minimizing spills and contamination. The right container should simplify your workflow, not complicate it.
Don’t forget to think about the overall design. Features like color-coded lids and ergonomic handles might seem trivial, but they add significant value by making the container user-friendly. In my experience, investing a bit more upfront for a high-quality container can pay off with improved safety and efficiency.
Proper Use and Maintenance of Oil Transfer Containers
Proper use and maintenance are the backbones of maximizing the benefits of Oil Transfer Containers. I’ve learned that even the best container can quickly become a source of trouble if not handled correctly. It all starts with understanding the proper use of these containers.
Before every use, I make sure that the container is clean and free from any residual contaminants. According to Precision Lubrication, neglecting this step can lead to contamination that affects the oil’s quality and the performance of your machinery citeturn0file0. I always follow a strict cleaning schedule, ensuring that the container is thoroughly washed and dried after every cycle.
The design of these containers is specifically meant to make cleaning easy. I use mild soap, warm water, and a soft brush to remove any grime without damaging the container’s material. It’s important to avoid harsh chemicals that could compromise the integrity of the plastic or metal. Regular cleaning not only keeps the oil pure but also extends the life of the container.
I also take extra care during the oil transfer process. Every time I open the container, I ensure that it’s done quickly and carefully to minimize exposure to dust and contaminants. This simple practice has saved me from many headaches, and I can’t stress enough how crucial it is to maintain a routine for both usage and cleaning.
Additionally, I always inspect the container for any signs of damage before and after use. A small crack or a loose lid can lead to significant issues, including leaks and contamination. If I find any damage, I replace the container immediately. This proactive approach has helped me avoid costly repairs and maintain operational efficiency.
Best Practices for Managing Oil Transfer Containers in Industrial Settings
In my journey to master oil transfer, I discovered that having a robust management plan for these containers is key. It’s not just about buying the right container, but also about how you manage it day in and day out. I’ve implemented several best practices that I’d like to share with you.
First, it’s essential to have a clear labeling system. I always label my containers with the oil type, grade, and the date of the last cleaning. This way, I can quickly identify which container is used for which lubricant and ensure that there’s no risk of cross-contamination. According to industry experts, proper labeling and color-coding are critical steps in container management.
Next, I establish a dedicated storage area for the containers. Keeping them in a well-organized and secure cabinet prevents them from being misplaced or damaged. This simple step has drastically improved the efficiency of my operations, as I no longer waste time searching for the right container.
Training the team is another crucial aspect. I make sure that everyone who handles oil transfers understands the importance of using these containers properly. We have regular training sessions that cover cleaning, storage, and proper usage techniques. This not only ensures safety but also helps in maintaining a high standard of quality in our operations.
Another best practice I follow is to conduct regular audits. I periodically sample the oil from the containers and compare it with the source oil to check for any contamination. If there’s a significant deviation, I take immediate action to clean or replace the container. This proactive approach has saved me from many potential issues that could disrupt operations.
Finally, I believe in continuous improvement. I regularly review and update our management plan based on feedback and new industry developments. Staying informed about the latest trends and technological advancements helps me keep our operations running smoothly and safely.
How I Implemented Oil Transfer Containers?
In my own experience, the transition to using dedicated Oil Transfer Containers was both a challenge and a revelation. At first, I was hesitant to invest in new equipment, but the benefits soon became evident. I recall the frustration of dealing with contaminated oil and the subsequent impact on machinery performance. That was my turning point.
I started by researching various options and speaking to experts in the field. I learned that not all containers are created equal and that paying attention to design, material, and functionality is critical. “According to Precision Lubrication, the right container can significantly reduce contamination risks,” I remember reading, and that really resonated with me.
After selecting the appropriate containers, I implemented a new management system. I set up a dedicated storage area and introduced a strict labeling system to keep track of each container. The initial effort was significant, but the results were clear: fewer spills, cleaner oil, and improved machine efficiency. Every time I see the pristine containers in our storage area, I’m reminded of how much our operations have improved.
Training my team was another essential step. I conducted hands-on sessions where I demonstrated the proper use, cleaning, and maintenance of the containers. The response was overwhelmingly positive, and the level of engagement from the team encouraged me to keep pushing for continuous improvement. Sharing these practices has not only enhanced our work environment but has also contributed to better overall performance.
Comparing Oil Transfer Containers with Traditional Methods
Before I switched to using Oil Transfer Containers, my team relied on traditional methods that were simply not up to the task. We often used open-top cans and makeshift containers that didn’t provide the necessary protection against contaminants. I remember the constant worry about oil spills and the time wasted cleaning up after every transfer.
Traditional methods are fraught with challenges. They leave room for error and expose the oil to airborne contaminants. In contrast, Oil Transfer Containers are designed specifically for this purpose. Their leak-proof design and controlled dispensing mechanisms make a world of difference in maintaining oil quality.
The transition wasn’t easy at first. I had to convince stakeholders that the upfront investment would pay off in the long run. However, the reduction in machine downtime and the prevention of costly repairs quickly justified the change. When I compared the two methods side by side, the benefits of the Oil Transfer Container were clear. It was not just about efficiency—it was about safeguarding our operations from preventable issues.
The Economic Benefits of Investing in Quality Oil Transfer Containers
One of the most convincing arguments I’ve encountered for using Oil Transfer Containers is the economic benefit they bring. I’ve seen how a single instance of contamination can lead to significant financial losses due to machinery downtime and repair costs. By investing in quality containers, you’re essentially safeguarding your bottom line.
In my own experience, the reduction in contamination-related issues has led to considerable cost savings. Fewer repairs and less frequent downtime mean that the operations run smoothly, ultimately improving profitability. According to industry insights, companies that adopt specialized oil transfer solutions report improved operational efficiency and cost-effectiveness citeturn0file0.
Moreover, the longevity of these containers contributes to long-term savings. A well-made Oil Transfer Container can last for years, even under harsh conditions. This durability means that the initial investment is spread over a long period, making it a smart financial decision. I have found that every dollar spent on proper equipment is returned manifold through the savings it generates.
Additionally, by reducing the risk of environmental hazards, you also mitigate potential legal liabilities and fines. The cost of environmental remediation can be astronomical, so preventing spills and leaks is not just about operational efficiency—it’s also about financial prudence.
Overcoming Challenges in Oil Transfer Container Management
Like any industrial solution, implementing Oil Transfer Containers comes with its own set of challenges. I’ve encountered issues such as improper handling, mislabeling, and even resistance from team members accustomed to old methods. However, these challenges are not insurmountable if addressed with a proactive approach.
One challenge I faced was ensuring that every team member understood the importance of proper container use. It required consistent training and a bit of a mindset shift. I organized regular workshops and created simple, clear guidelines to help everyone understand the benefits and proper practices. This approach helped to create a culture of accountability and care.
Another challenge was keeping up with regular maintenance. Even the best containers need routine cleaning and inspection to perform at their best. I implemented a schedule that everyone in the team could follow, ensuring that no container was ever neglected. This routine not only kept the oil pure but also extended the life of the containers, making the entire system more reliable.
Dealing with these challenges taught me the value of perseverance and continuous improvement. Every obstacle was an opportunity to refine our processes and enhance our operational efficiency. I learned that success in industrial operations often hinges on the details, and paying attention to these small things can lead to big improvements over time.
Environmental and Safety Implications
One of the aspects that truly motivates me is the environmental benefit of using Oil Transfer Containers. In today’s world, where sustainability is more important than ever, every little step counts. Clean and efficient oil transfer processes not only protect our machinery but also prevent harmful spills that can damage the environment.
I always feel a sense of responsibility knowing that by using the right container, I am contributing to a safer environment. Properly managed oil transfer minimizes the risk of leaks and spills that can contaminate soil and water. According to environmental guidelines discussed by industry leaders, using leak-proof containers is essential in reducing environmental hazards.
Safety is another critical benefit. I have witnessed accidents caused by improper oil handling, and these incidents have reinforced my commitment to using the correct tools. Oil Transfer Containers, with their secure lids and controlled dispensing systems, significantly lower the risk of workplace accidents. This not only protects the workers but also ensures that operations run without interruptions caused by safety incidents.
Furthermore, by maintaining high standards in oil handling, companies can comply with various occupational health and safety regulations. This compliance not only avoids legal issues but also builds a reputation for reliability and care. I always make sure that our practices align with industry standards, which gives me confidence in the long-term sustainability of our operations.
Embracing Innovation and Continuous Learning
One thing that has always driven my passion for improvement is the pursuit of innovation. I constantly seek out new techniques and technologies that can make oil transfer safer, cleaner, and more efficient. The landscape of industrial operations is always evolving, and staying informed about the latest advancements is crucial.
I regularly attend industry seminars and read up on new research in the field of lubrication and oil management. This continuous learning process has introduced me to concepts like automated cleaning systems and smart containers that monitor oil quality in real time. These innovations are transforming the way we handle lubricants, making it easier to maintain a high level of operational efficiency.
The feedback from colleagues and industry experts has been invaluable in this journey. Sharing experiences and success stories not only inspires me but also helps spread best practices throughout the community. I believe that collaboration and a willingness to embrace change are the keys to staying ahead in any industry.
Final Thoughts and Conclusion
After exploring the world of Oil Transfer Containers, I can confidently say that these tools are indispensable in modern industrial operations. From preventing contamination and ensuring safety to improving efficiency and saving costs, the benefits are clear. I’ve seen firsthand how switching to specialized containers can transform an entire operation, reducing risks and streamlining processes.
In this guide, we’ve covered what an Oil Transfer Container is, its various design features, the benefits it offers, and best practices for its management. I’ve also shared personal experiences and real-world examples that highlight the practical advantages of using these containers. Whether you’re new to the field or looking to upgrade your current practices, I hope you find these insights helpful and actionable.
I encourage you to take a closer look at your own oil transfer processes. Consider what improvements can be made and whether investing in high-quality Oil Transfer Containers could be the solution you’ve been searching for. The journey to cleaner, safer, and more efficient operations starts with the right tools and a commitment to excellence.