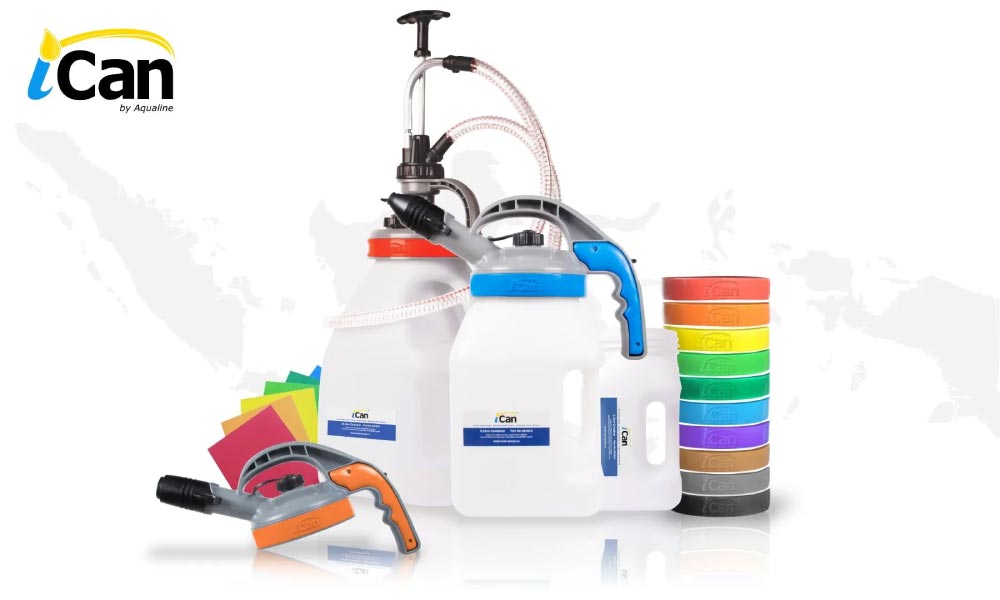
Oil Container: Definition, Function, and Its Role in the Industry
In today’s fast-paced industrial landscape, the efficient storage and transportation of oil and its derivatives is paramount to ensuring smooth operations across multiple sectors. Oil containers serve as the backbone of this logistical process, playing a critical role in maintaining the integrity and safety of oil during storage and transit. Whether you’re involved in the energy sector, automotive manufacturing, or chemical processing, understanding the intricacies of oil containers can provide key insights into operational efficiency and risk management. In this article, we delve into the definition, function, and overall significance of oil containers in the industry, exploring their evolution, types, materials, and future trends.
What is an Oil Container?
Definition of Oil Container
An oil container is a specialized vessel designed to store, transport, and manage oil along with its by-products. Constructed to meet rigorous safety and quality standards, these containers ensure that oil remains uncontaminated and secure throughout its journey from production sites to end users. Whether it is a drum, tanker, or a pressurized container, each type is engineered to address specific needs and challenges in the oil industry.
A Brief History of Oil Containers
The concept of oil containers dates back to the early days of the industrial revolution. Initially, simple metal drums were used to store oil, but as the demand for oil increased, so did the need for more robust and efficient storage solutions. Over the decades, advancements in metallurgy and engineering led to the development of various container types capable of handling larger volumes and offering enhanced safety features. Today, modern oil containers incorporate advanced materials and technology, reflecting a history of continuous innovation and adaptation to industry demands.
Types of Oil Containers
Oil Drums
Oil drums are among the most common forms of oil containers used today. Typically made from high-quality steel or durable plastics, these drums are designed to store oil on a small to medium scale. Their relatively compact size and ease of handling make them ideal for use in refineries, small-scale storage facilities, and during transportation in localized areas.
Tankers
Tankers are massive oil containers used primarily for the transportation of large volumes of oil, especially via maritime routes. These specialized vessels are equipped with state-of-the-art safety systems and are engineered to maintain the oil in optimal conditions over long distances. Tankers play a critical role in the global oil supply chain, enabling the movement of oil from production regions to consumer markets across the world.
Pressurized Containers
Pressurized containers are specifically designed for storing oil or gas products that require maintenance under controlled pressure conditions. These containers are often employed in the chemical and energy sectors, where the preservation of product integrity under variable pressure is crucial to preventing leaks or hazardous incidents.
Functions of Oil Containers in the Industry
Storage and Transportation
The primary function of oil containers is to securely store and transport oil from one location to another. By offering a range of sizes and capacities, these containers provide flexibility to meet various logistical requirements. Whether oil is being moved from extraction sites to refineries or from refineries to distribution centers, oil containers ensure that the product reaches its destination safely and efficiently. Imagine the complexity behind ensuring every drop of oil is accounted for during transit—this is where the reliability of oil containers becomes indispensable.
Safety and Operational Efficiency
Beyond simple storage and transport, oil containers contribute significantly to operational safety. Their robust design and adherence to international safety standards help prevent oil spills, leaks, and other hazardous incidents that could lead to substantial financial losses or environmental damage. Additionally, modern oil containers are designed to facilitate rapid loading and unloading, thereby enhancing overall operational efficiency and reducing downtime in the supply chain.
Materials and Technologies in Oil Container Manufacturing
Materials Used in Production
Modern oil containers are manufactured using a variety of high-quality materials to ensure durability and resilience. Common materials include stainless steel, aluminum, and specialized polymers. These materials are chosen for their resistance to corrosion, ability to withstand extreme temperatures, and overall structural strength. The selection of appropriate materials is critical as it directly affects the container’s longevity and performance in various environmental conditions.
Technological Innovations in Manufacturing
Technological advancements have transformed the way oil containers are designed and manufactured. Today, many containers come equipped with digital sensors that monitor parameters such as pressure, temperature, and structural integrity in real time. The integration of Internet of Things (IoT) technology enables operators to remotely track the status of containers, ensuring swift responses to potential issues before they escalate. This blend of traditional engineering and modern technology not only enhances the safety and reliability of oil containers but also contributes to cost savings by reducing maintenance requirements and preventing accidents.
Role of Oil Containers Across Different Industries
Energy Sector
In the energy sector, oil containers are indispensable. They are used to store and transport crude oil, refined petroleum products, and various chemical derivatives. Efficient storage and timely transportation are vital for the smooth operation of refineries and power plants. The strategic use of oil containers helps companies maintain adequate inventory levels and minimize the risks associated with oil spills and other hazardous incidents.
Automotive Industry
The automotive industry relies heavily on oil containers for the storage of lubricants, engine oils, and other vital fluids required in the manufacturing and maintenance of vehicles. Given the high standards required for automotive components, the quality and integrity of these oil products are paramount. Oil containers in this sector are designed to prevent contamination and ensure that the lubricants perform optimally, thereby extending the lifespan of vehicle engines and reducing maintenance costs.
Manufacturing Sector
Oil containers also find extensive application in the manufacturing sector. They are used to store various oil-based products such as hydraulic fluids, greases, and other lubricants essential for operating heavy machinery. The reliability of oil containers ensures that production lines run smoothly without unexpected interruptions due to fuel or lubricant shortages. Moreover, by maintaining the purity and quality of the stored products, oil containers contribute to higher overall production quality and efficiency.
Standards and Regulations in Oil Container Usage
National and International Standards
The design, manufacturing, and usage of oil containers are governed by a myriad of national and international standards. Regulatory bodies, both locally and globally, have established strict guidelines to ensure that oil containers meet safety, environmental, and operational requirements. In many countries, organizations such as the International Organization for Standardization (ISO) set benchmarks that manufacturers must adhere to, covering everything from material quality to performance testing. Compliance with these standards is crucial for preventing accidents, protecting the environment, and ensuring smooth international trade.
Advantages of Modern Oil Containers
Cost Efficiency and Operational Benefits
One of the primary advantages of modern oil containers is their ability to enhance cost efficiency. By reducing the likelihood of oil spills, leaks, and other operational mishaps, these containers help companies save on cleanup costs, legal liabilities, and downtime. Additionally, the streamlined design of contemporary containers allows for faster loading and unloading processes, thereby reducing labor costs and improving overall supply chain efficiency. In a competitive market, every minute saved translates into significant cost reductions and increased profitability.
Enhanced Safety and Environmental Impact
Modern oil containers are engineered with an emphasis on safety and environmental sustainability. Advanced sealing mechanisms, real-time monitoring systems, and durable construction all contribute to minimizing the risk of accidental spills and leaks. This not only protects the environment from contamination but also safeguards the health and safety of workers involved in oil transportation and storage. As environmental regulations become increasingly stringent, the role of safe and eco-friendly oil containers has never been more critical.
Challenges and Solutions in Oil Container Management
Logistical and Security Challenges
Despite the many advantages, managing oil containers is not without its challenges. Logistical issues, such as long-distance transportation and handling in remote areas, can complicate the storage and movement of oil. Furthermore, the risk of theft, damage during transit, and exposure to extreme weather conditions add layers of complexity to oil container management. Operators must be vigilant and proactive in addressing these challenges to avoid costly disruptions and ensure the safety of both the product and the environment.
Technological and Operational Solutions
To overcome these challenges, the industry has embraced a variety of innovative solutions. The implementation of advanced tracking systems, digital sensors, and automated monitoring platforms has revolutionized how oil containers are managed. These technologies enable real-time oversight, allowing operators to identify and address potential issues before they escalate. Additionally, rigorous training programs and standardized operational procedures have been established to ensure that personnel handling these containers are well-equipped to manage risks. Such proactive measures not only improve safety but also enhance overall operational efficiency.
Conclusion
Oil containers are a fundamental component of modern industrial operations, serving as the linchpin in the safe storage and efficient transportation of oil products worldwide. From their humble beginnings as simple metal drums to today’s technologically advanced systems, oil containers have evolved significantly, reflecting the continuous drive for improved safety, cost efficiency, and environmental protection. Their role spans across various industries—from energy and automotive to manufacturing—underscoring their critical importance in maintaining the stability and reliability of global supply chains.